Tube Furnace
Features
- Maximum operating temperature range up to 1800°C.
- Available in, Horizontal operation, Vertical operation, universal operation.
- Compact design for minimum space requirement.
- Rugged and durable Construction.
- Outer casing is made up thick mild steel with duly powder coated or thick buffed stainless steel, gives long service life with extremely resistant.
- Multilayer insulation with vacuum formed ceramic fibre or refractory bricks with low thermal mass.
- Alumina/Quartz/Metal tube with two fibre plugs included.
- Inner diameter of the tube from 20mm to 150mm.
- Heated Length from 100mm to 2000mm.
- Furnace design with powerful heating elements i.e. FeCrAl, SiC and MoSi2 in all sides of the work tube providing fast heating rate.
- Fast heat up and cool down rates.
- Temperature uniformity +/- 5°C.
- Temperature control with PID controllers.
- Power control with solid state relays or Thyristor units for very precise temperature Control, wear-free and noiseless.
- High mechanical durability, short heating cycle and low power consumption.
Optional
- Multi-zone temperature control.
- Touchscreen temperature controller.
- Over Temperature/Over Current Limiter.
- Vacuum pump with fittings
- Gas and Vacuum Compatible Flanges, Water cooled flanges with chiller.
- Door flanges with hinges.
- Gas mixing system.
- Digital/Analog flowmeters.
- Port for additional thermocouple on the flange.
- Process observation window on flange.
- Buzzer, Digital timer, Emergency shut down.
- Data Recorder.
- RS232/RS485/USB interface.
- Calibration of temperature measurement systems.
- Table/Stand for supporting the systems.
- Data Acquisition System (DAS) through software.
- UPS Systems.
- Customization as per user requirement.
- Caster wheels with brakes.
Applications
Tube Furnaces are designed for R&D labs, Educational institutions, Medicine and Industry, Chemical Industries, Ceramics Industry, Biomedical Industry, Pharma Industry, Thermal Process Technology, Advanced Materials for following applications:
Purification, Coating, Drying, Hardening or Ageing of samples, Annealing, Brazing, Calcination, Degassing, Sintering, Tempering, Thermocouple calibration, Testing of fuel cells, Catalyst research, Inorganic and Organic purification, Coating etc.
Specification Sheet
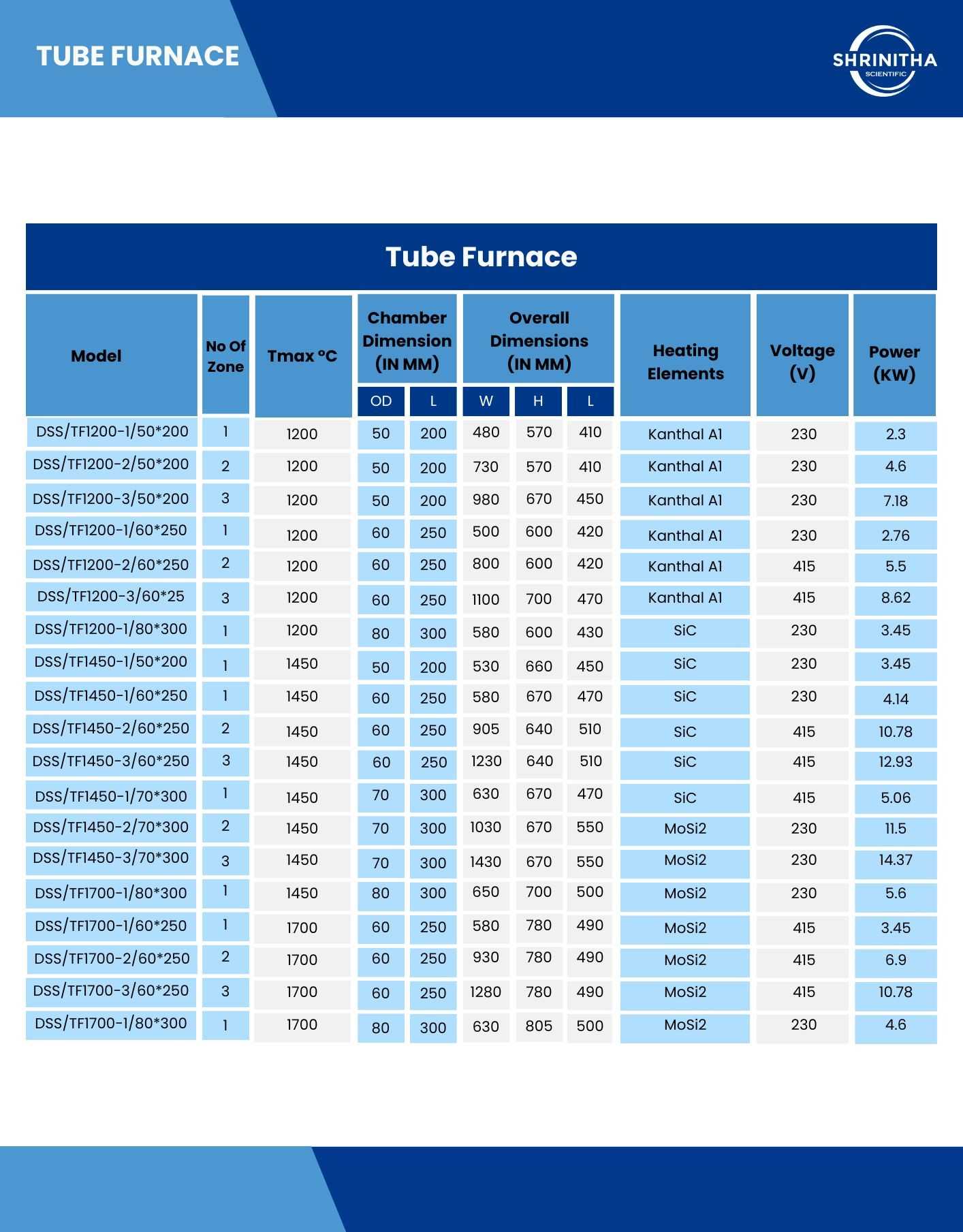
Products Gallery
Our Expertise’s
Precision Engineering
Innovative Solutions
Quality Assurance
Customer
Focus